Clinical engineers are problem solvers. Whether they are in hospitals, private practices, or industry settings, they work with complex human and technological systems. These hard-working individuals tend to wear a lot of hats, including technology managers for medical equipment systems.
- Medical Device Maintenance
- The Challenges of Asset Tracking
- Asset Tracking using BLE
- Solving Problems
- Reducing Costs

Hospital-based clinical engineers are responsible for making sure medical devices are effective, safe, and accounted for. They handle service contract management, the data processing systems necessary for the management of medical equipment, and coordinate not only service agreements but internal operations too. On top of all that, they’re responsible for ensuring complete compliance with all laws and regulations governing medical devices with the Joint Commission, the Centers for Medicare and Medicaid Services, and more.
Medical Device Maintenance
Maintaining medical devices relates to all activities needed to keep them operating at an adequate level and minimizing any downtime in their use. The responsibility involves both corrective and preventive maintenance. Preventive maintenance (PM) for medical devices are handled as scheduled events. The devices need to be evaluated for the frequency of relative maintenance and the impact on patient care if the device fails.
There are also required inspections to coordinate. Every piece of equipment entering a hospital or other medical facility requires an inspection before it can be used. They must ensure each device operates safely and performs as promised.
If this sounds like a tall order, it is. For a hospital or medical facility to offer quality patient care, the equipment used must be regularly monitored, serviced, and if necessary, repaired or replaced while maintaining complete compliance.
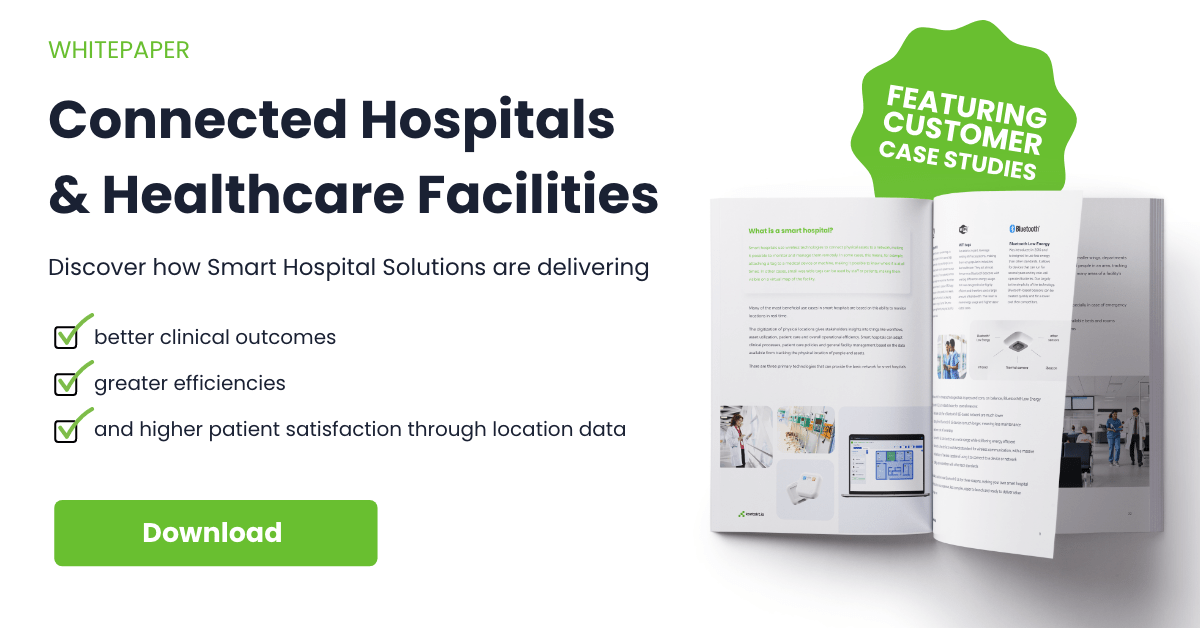
The Challenges of Asset Tracking
To be able to coordinate a successful medical device maintenance program, clinical engineers use a computerized maintenance management system (CMMS) as a tool in documenting regulatory compliance. These systems are constantly improving and a great help in keeping up with the latest laws and regulations governing compliance. But there’s another problem to solve: knowing where every single device is at any given time.
Tracking assets is a vital part of medical device maintenance. By knowing exactly where equipment is when you need it, you save time, better manage your staff, and, most importantly, place the focus on patient care where it belongs.
In a hospital with a high volume of medical devices, a thorough inventory with no visibility can take as long as eight to ten weeks each year without a guaranteed 100% search rate. Up to four to seven hours can be spent each day and as many as 1,200 to 2,000 hours can be lost annually for just one preventive maintenance event.
Frequently used devices like portable ultrasound devices, infusion pumps, and even wheelchairs can move several times in a single day throughout a facility. Time spent looking for these devices is time that could be spent providing the best possible care to the patient who needs them.
One solution would be to invest in additional pieces of equipment but that just increases the workload and hurts your bottom line. If you can’t track wheelchairs, you may not realize you don’t need to order more. There may be a surplus in one area of the facility and a constant shortage in another.
With proper asset tracking, there’s a quick and easy fix. Without it, you may end up ordering more and overstocking. And wheelchairs are just one example of medical devices that could be underestimated and stocked improperly.
Another solution is one that can be used to easily locate and track medical devices in real-time using established wireless access points combined with Bluetooth-enabled tags and a convenient app on a mobile device or phone.
Asset Tracking using BLE
To help with asset tracking, many innovative new methods have come along including Barcode, IoT, NFC, QR code, RFID, and Bluetooth Low Technology (BLE). While each of these methods has grown and adapted with use, the best solutions for asset tracking are the ones that provide real-time information.
Fast Device Location
Kontakt.io uses tracking tags with BLE devices inside them to pinpoint locations relative to access points placed strategically through a hospital or medical facility. The location is sent to the CMMS used and anyone authorized to access that software. Unlike RFID tags that have to be scanned by a human or checkpoint scanner, BLE tracking tags provide continuous updates on items the software it’s integrated with.
Setting Minimum and Maximum PAR Levels
A periodic automatic replenishment (PAR) level is an inventory of all items and devices you have on hand at any given time. Along with this, it’s important to understand how many units you need of any particular medical device in your department. Many use their best estimate of how many items they need daily. BLE trackers feed information into the software used to provide you with exact numbers on the minimum and maximum levels you need of any device in a given department based on average daily usage.
This also helps immensely when it comes to managing inventory. Using the data from BLE trackers, you can set PAR levels to lower and upper ranges of usage during a normal working day. This will give you a highly accurate account of how many devices you need.
Maintaining Inventory PAR Levels
Clinical engineers can use Kontakt.io solutions to review available device locations, including those closest to the seeker if badges are also distributed to staff. PAR levels can be monitored and recommendations made based on current conditions in the hospital or facility.
If any inventory item is above the maximum needed for an area, the staff knows which department they can grab an infusion pump from to replenish their own inventory. The retrieval is noted within the system for efficiency. If another department has less than what they need for wheelchairs, they are notified so they can replenish their stock before needs become urgent.
Loss Prevention
Not only can BLE trackers send information on minimum and maximum PAR levels, they can also let you know if any item has been removed from an authorized area. If someone leaves a facility with a wheelchair, you’ll be notified immediately. This will help cut down on shrinkage due to theft. That improves your budget and keeps you from being short a vital item until a replacement can be ordered.
Hospital buildings have significant foot traffic at entrances and exits with multiple team members and vendors transporting various materials needed for patient care; and processing laundry and trash. Such high-volume activities result in involuntary negligence leading to unintentional loss of expensive medical devices and wheelchairs.
The problem is greater with small medical devices that tend to get wrapped up without notice in soiled linens or in trash bags that leave the hospital; and are never recovered again. A conservative estimate of 2% loss of devices in a typical 300 bed hospital results in an annual impact of about $200,000. This does not account for indirect losses related to absence of a medical device at the point of care when needed. Delayed treatment results in dissatisfied patients and lower reimbursements. Not knowing exactly if the device is in the building or lost may also cause accounting implications and unnecessary maintenance support costs adding strain to the clinical engineering department.
BLE trackers are available in extremely small form factors and can be attached on small devices that tend to get lost often. Beacons strategically placed in rooms capture restricted movement before it is too late. Notifications can be provided in the form of local audiovisual alarms as well as via mobile devices to alert well intentioned staff to recover items on time. BLE trackers are also read via mobile devices to isolate trash and laundry bags where the device may be hidden for rapid and safe recovery.
Maintain Compliance
Every 36 months, surveyors from the Joint Commission visit accredited health care facilities to ensure compliance. These unannounced visits are called surveys. The Joint Commission sends health care professionals, experts in their fields, to conduct the survey.
The surveyors randomly select patients and review their medical records to make sure any and all applicable compliance standards were met. Not only will they talk to any doctors or nurses who provided care, they’ll speak with the patients too.
In order for proper care to be given as soon as possible, equipment for diagnostic tests and other needs must be ready and available. Any inability to locate a medical device can cause a delay in providing patient care and potentially have a negative impact on facility compliance. The result can be fines or even loss of accreditation.
Solving Problems
Using BLE technology from Kontakt.io, medical device maintenance and management is greatly improved for the clinical engineers responsible for them. Asset tracking helps clinical engineering staff to optimize their responsibilities and operate more efficiently. They spend less time tracking down devices, managing inventory, and monitoring PAR levels. They can devote their time to providing excellent patient care.
Productivity is increased and that leaves more time for clinical engineers to solve other problems, like cybersecurity threats, repairs, and required service swiftly. Kontakt.io solutions provide the information clinical engineers need to meet any and all applicable compliance laws and regulations.
Using BLE technology is highly accurate and less expensive than either WiFi, passive or UWB tag solutions. Kontakt.io provides comprehensive Asset Tracking and Management applications that not only enable clinical engineers to rapidly search devices but complement CMMS in providing data analytics driving financial decisions related equipment purchase, maintenance contract negotiations, rentals and balancing useful life of assets with depreciation. Application can also be used to track staff, patients, and more for a more efficient, safer environment.
Reducing Costs
Asset tracking solutions using BLE technology are gaining in popularity. Bluetooth offers a quality alternative to active RFID tags. Advantages BLE offers over RFID open source, interoperability, scalability and lower total cost of ownership. BLE data backhaul is over existing WiFi access points eliminating the need for an alternative network, a significant cost burden for traditional active RFID. Location detection is driven by plug-and-play beacons that are one-tenth the cost of traditional active RFID location detectors. Since BLE radio is designed to consume low power, batteries can be off-the-shelf and last longer than active RFID. BLE is also extremely effective compared to passive tag solutions which require a large number of POE connected readers throughout the hospital to provide real-time location updates and have a significant installation burden that requires skilled labor.
The open source nature of BLE streaming protocol allows various applications to consume the data stream for solving specific problems giving the customer an option to choose a solution that fits their needs effectively.
Conclusion
Medical device management can be dramatically streamlined through the use of Kontakt.io’s new Portal Beam. It’s a low-maintenance, low-energy sensor that drives better clinical outcomes by providing insights into environmental conditions that can impact patient well-being.
With Portal Beam, you can get instant insights into how space is being used in your facility, cutting time spent on locating free rooms and beds. Air quality and temperature, humidity, light conditions and carbon dioxide levels can all be monitored and alerts set when parameters are broken. On top of all that, patient locations can be tracked to ensure their safety and facility security.
Portal Beam is powered by the Kio Cloud, which streamlines data from multiple devices, applying artificial intelligence in continually-improving location accuracy and precision and acting as a single integration point to our end user apps and 3rd party systems like CMMS, MR and BMS.
Kio Cloud makes it possible to increase efficiency and asset utilization in several ways. Multiple aspects of healthcare facility management can be optimized through leveraging the insights that come with real-time location tracking:
- Cut time spent on searching for devices and other assets
- Accelerate cleanroom PAR restocking
- Reduce dwell time of equipment waiting for cleaning
- Enable better loss prevention
- Streamline bed and wheelchair management
Kio Cloud provides more value through the ability to scale other solutions that impact other aspects of patient outcomes, including staff duress situations, patient tracking and temperature monitoring. Contact us today to learn what we can do to improve your hospital or medical care facility with affordable, effective location services.

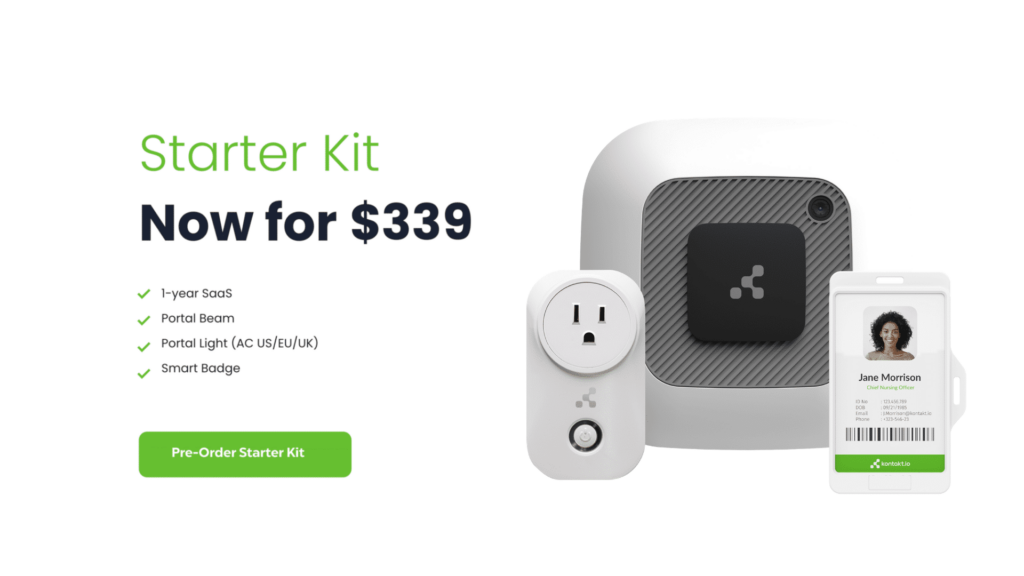