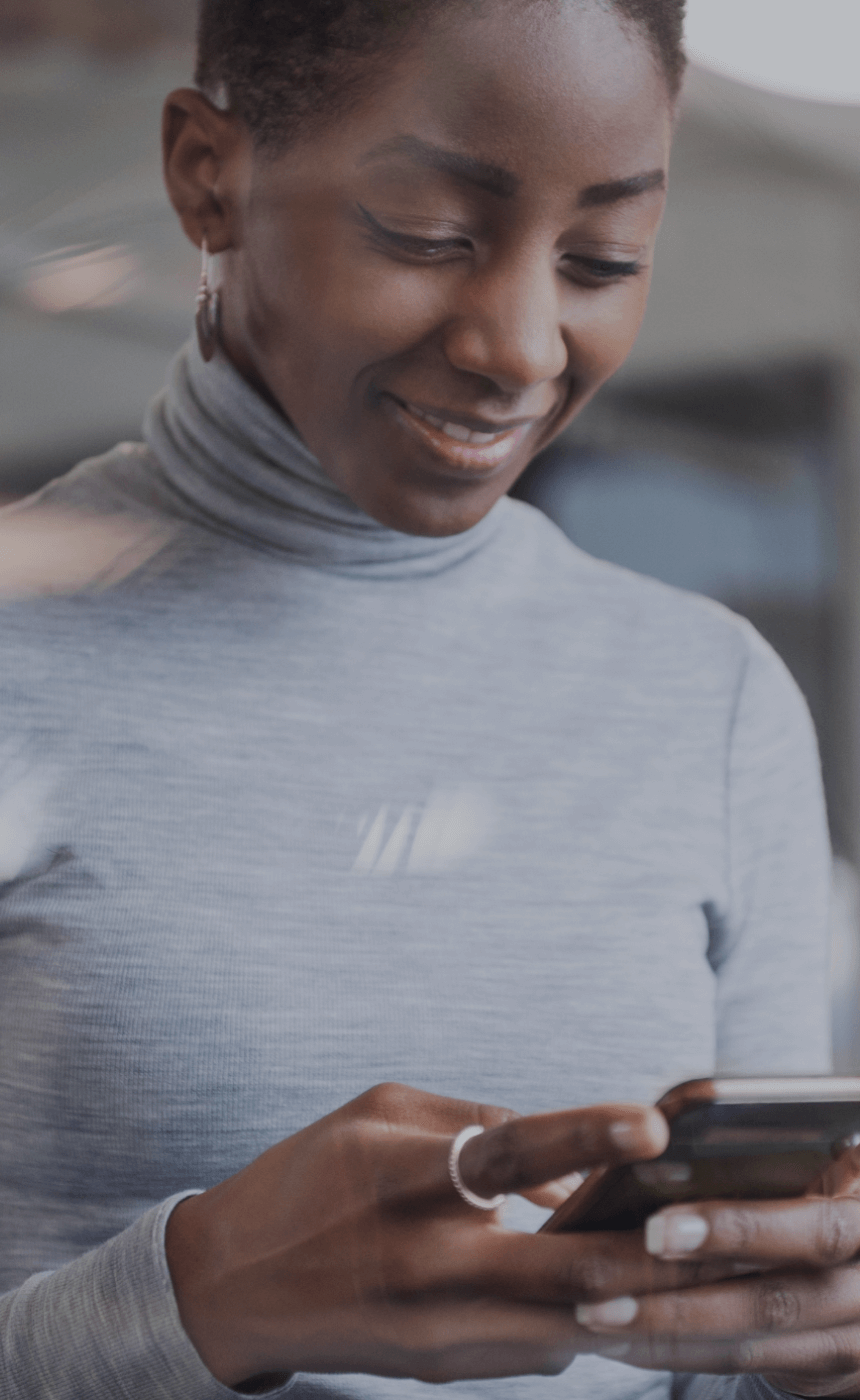
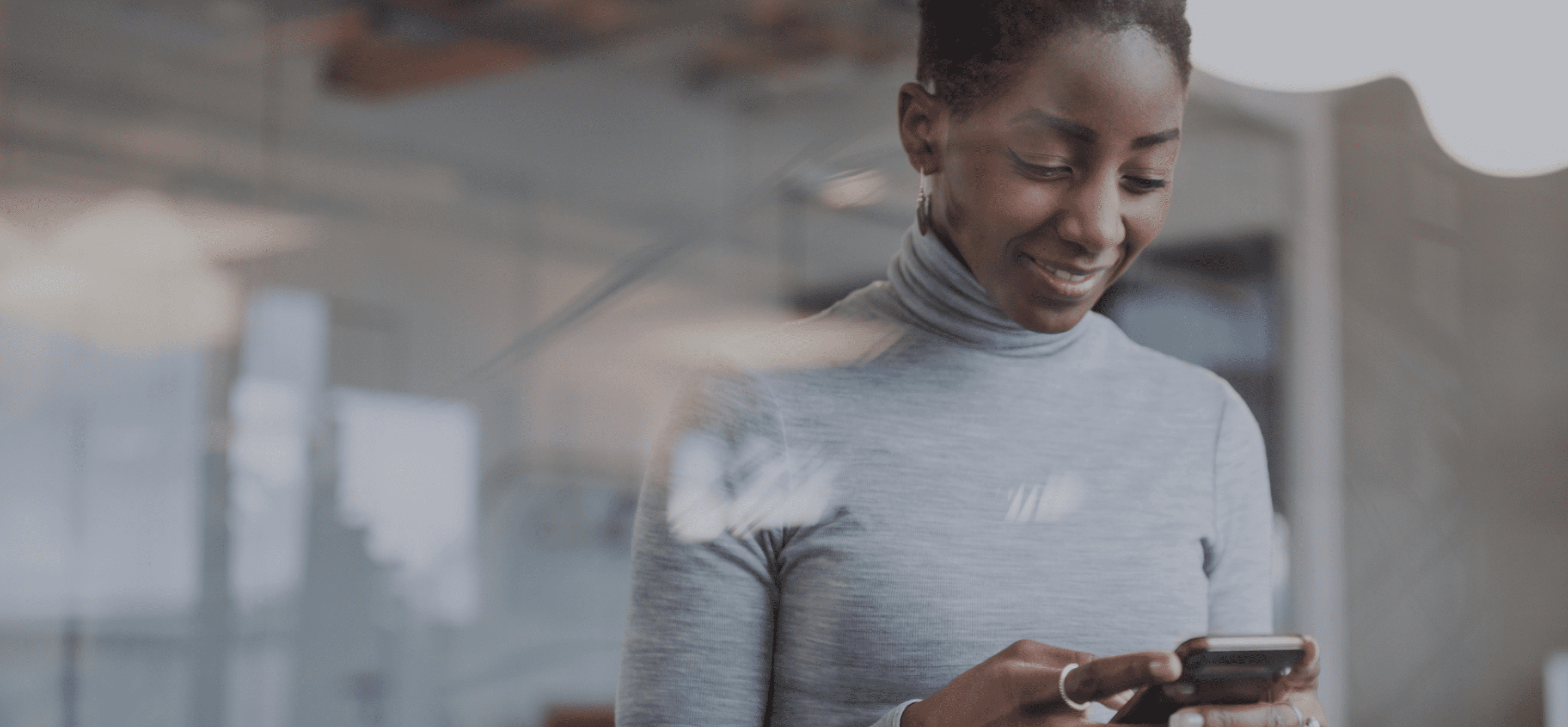
Kontakt.io Content Hub
Browse our ever-expanding library of articles, webinars, and white papers for expert insights.
What are you interested in?
Format
Industry
Topic
Clear filters
Search results for:
No results
Healthcare
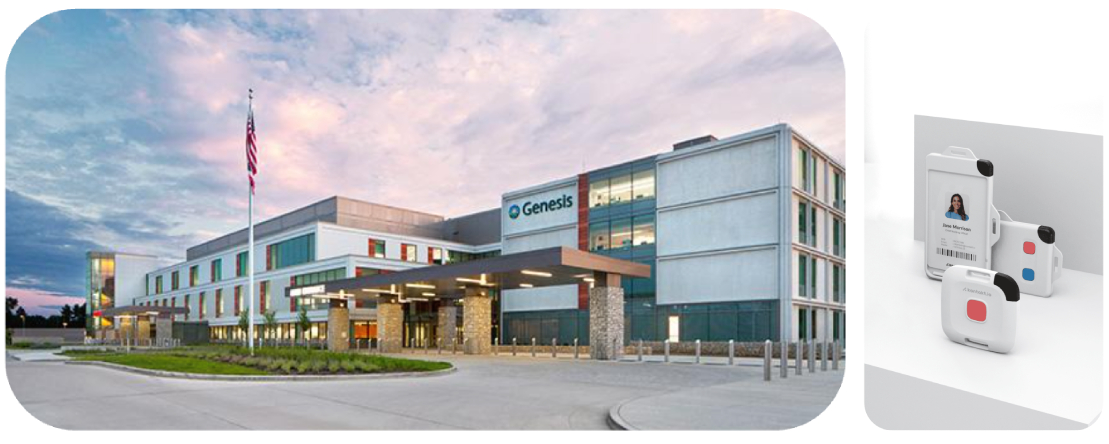
Blog
July 15, 2025
Customer Success: Genesis HealthCare System Redefining WPV Incident Response
View Now
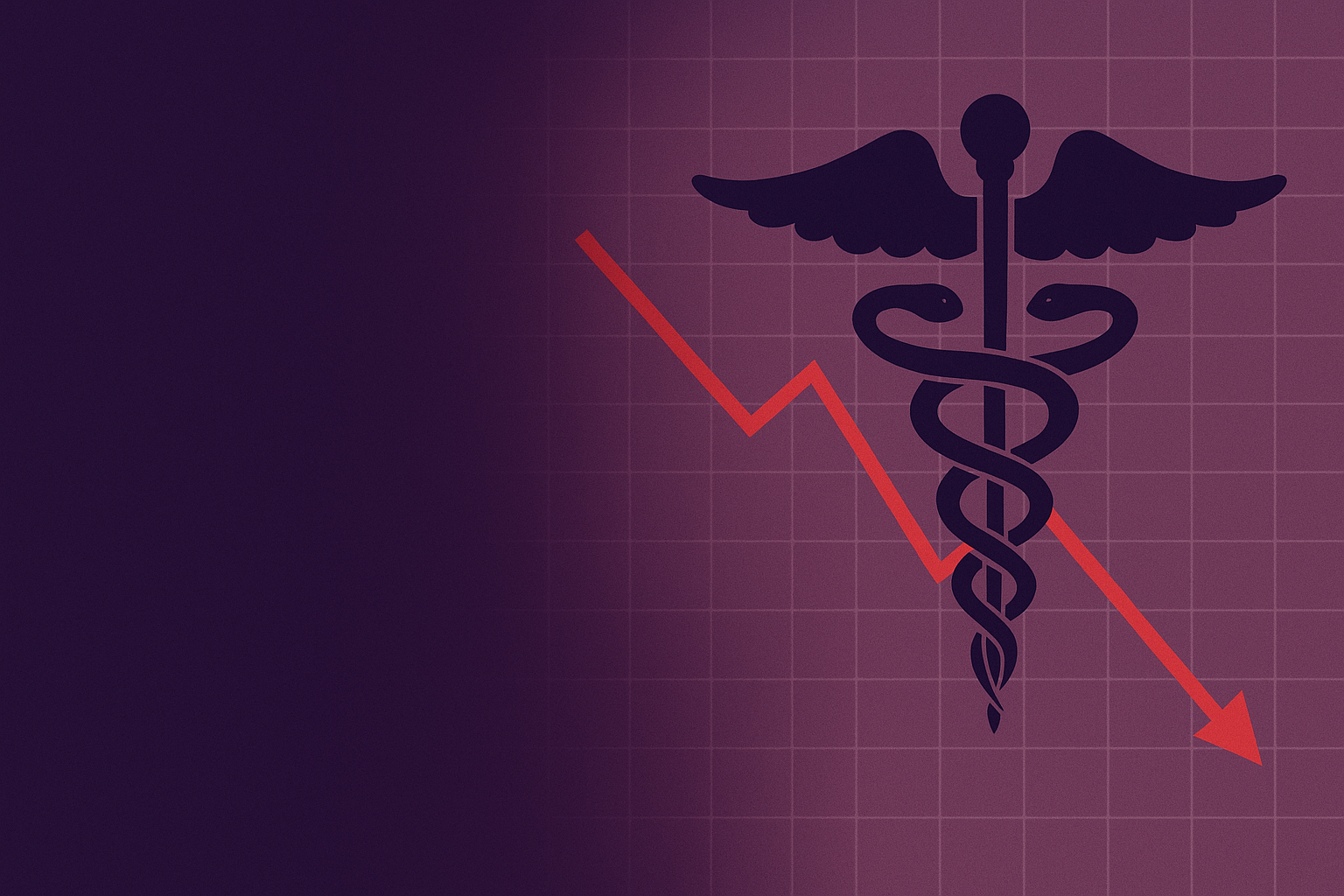
Blog
July 10, 2025
Breaking Free from Stagnation: A CEO’s View on Hospital Operations
View Now
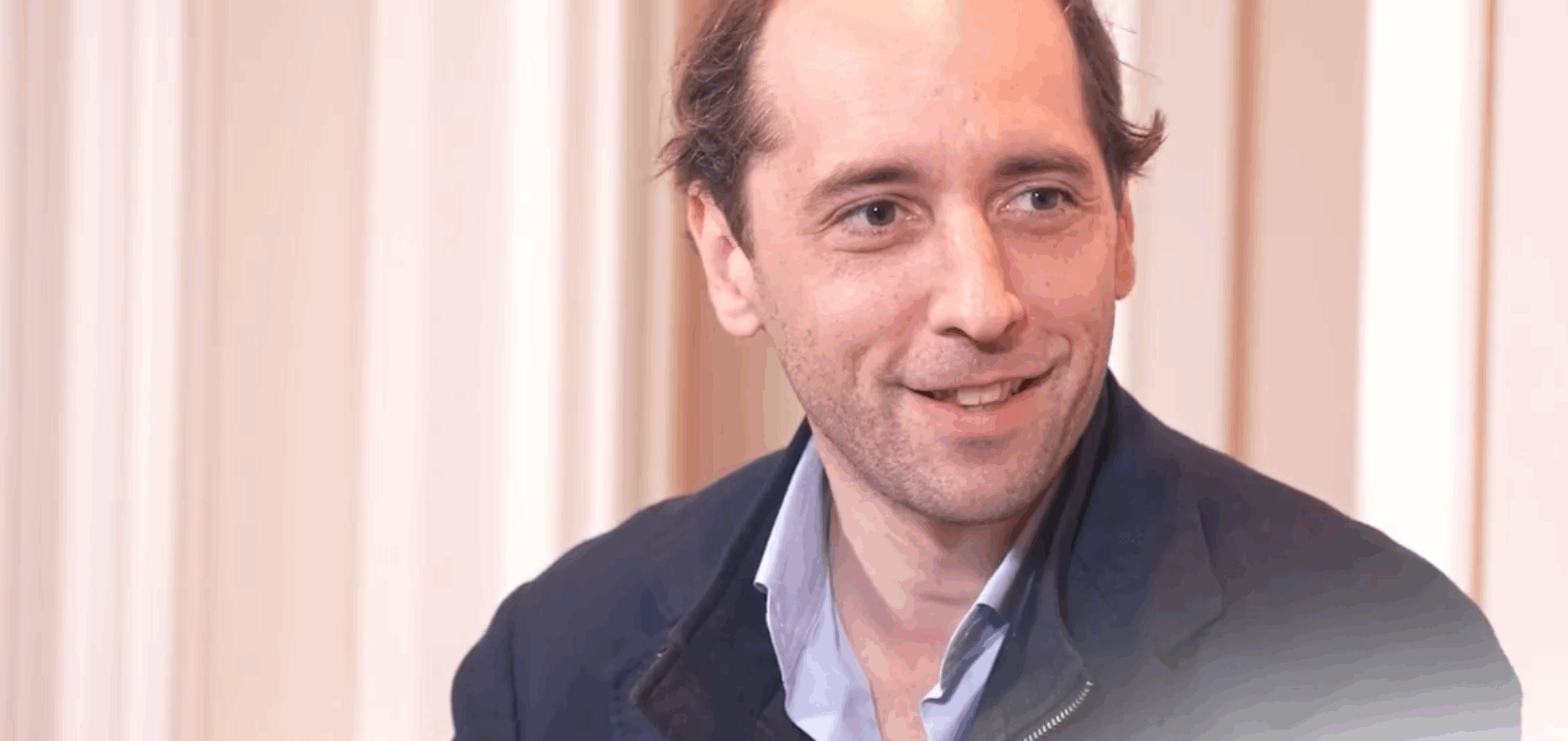
Blog
June 30, 2025
Kontakt.io CEO on HIMSS TV: Managing Resources with Agentic AI Can Boost Operational Efficiency
View Now
Page
1