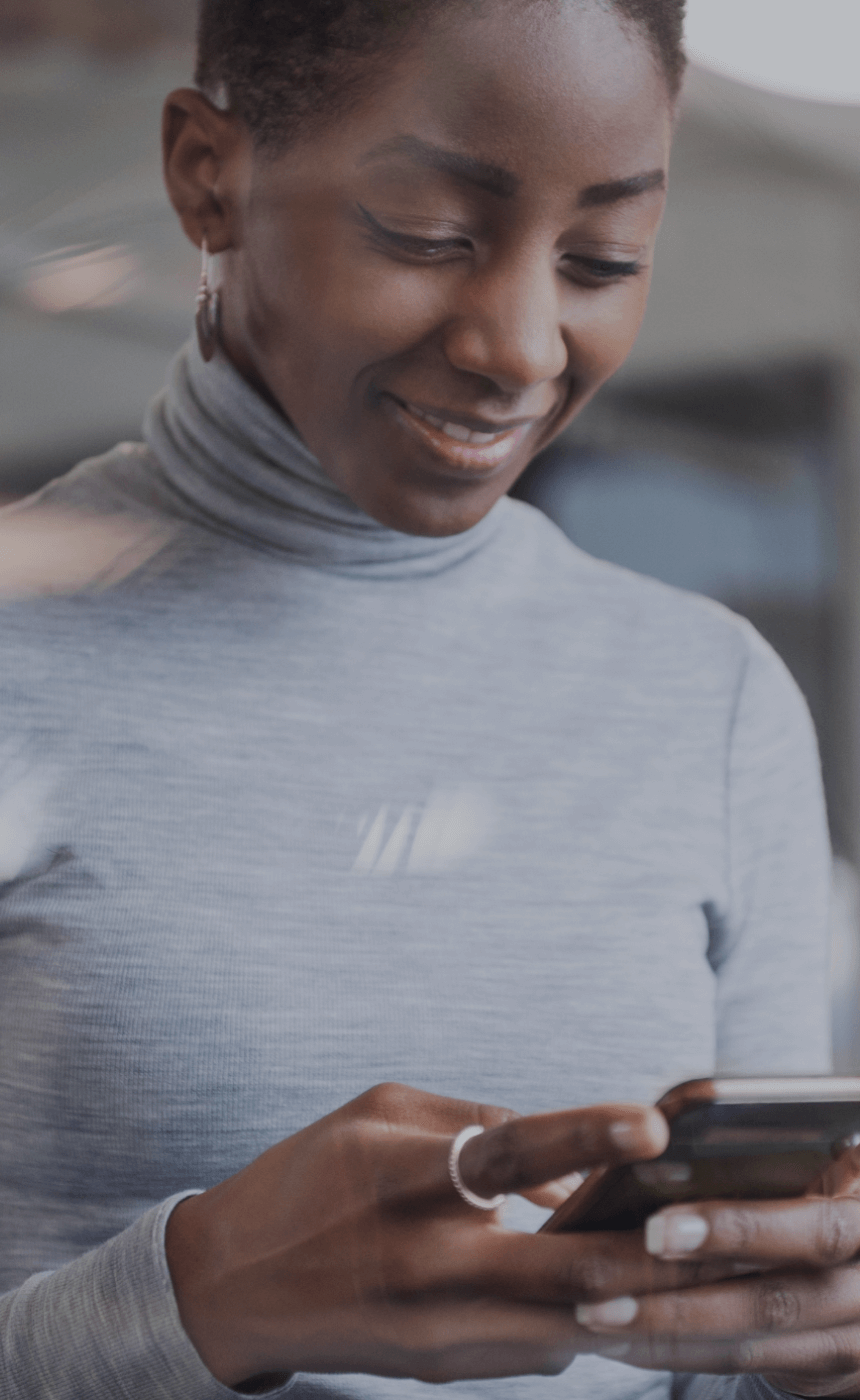
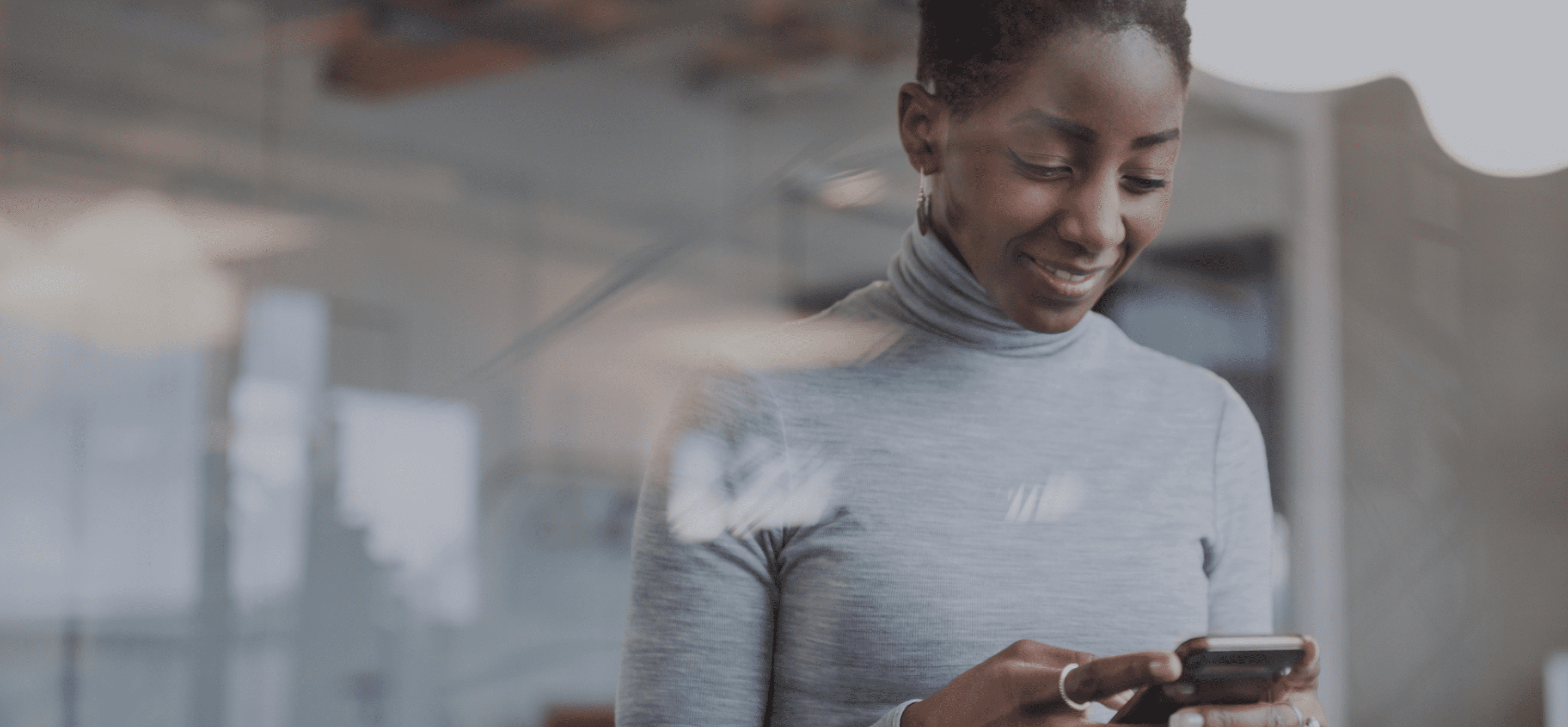
Kontakt.io Content Hub
Browse our ever-expanding library of articles, webinars, and white papers for expert insights.
What are you interested in?
Format
Industry
Topic
Clear filters
Search results for:
No results
Healthcare

Blog
June 24, 2025
AI Agents in Healthcare: Facts and Fiction
View Now
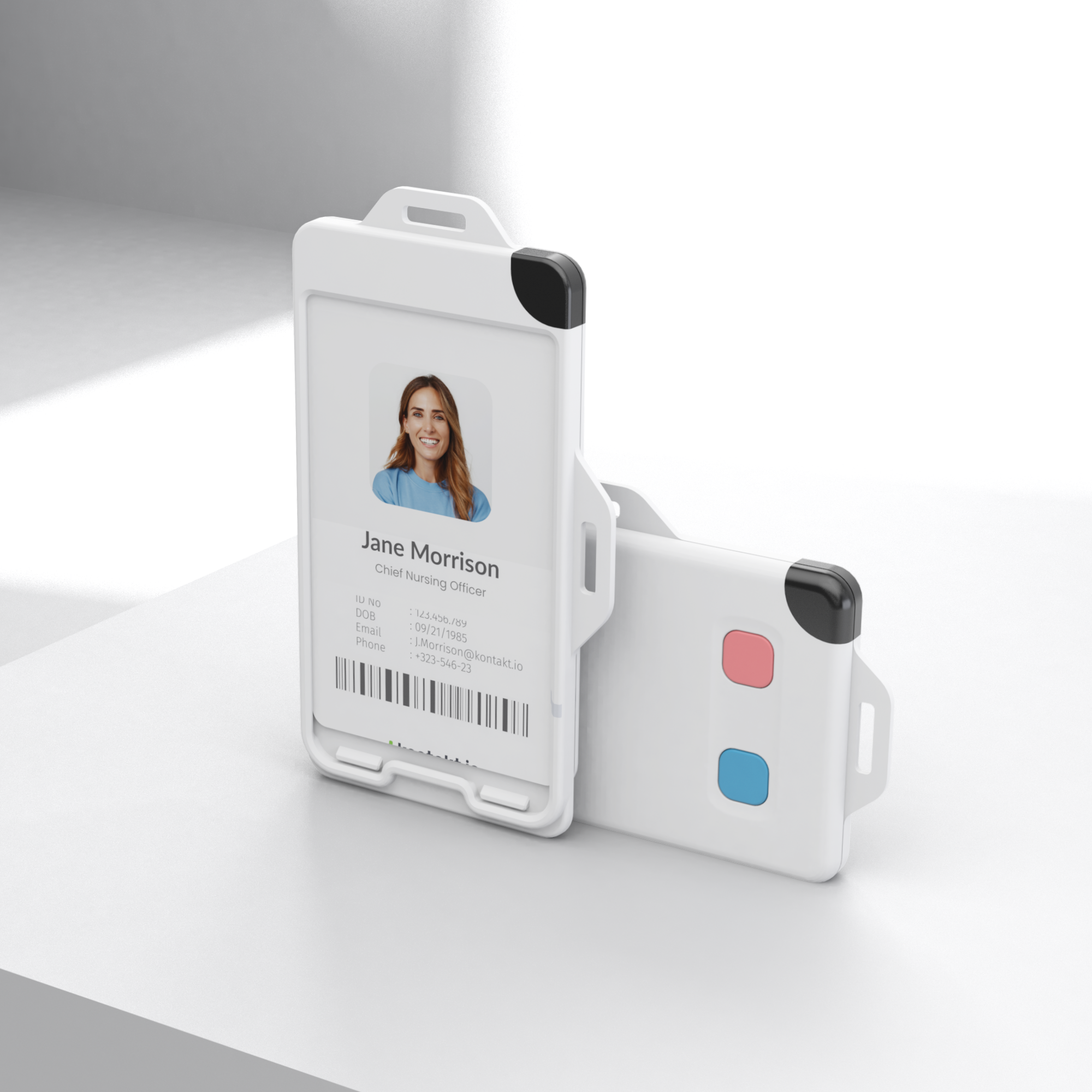
Blog
June 18, 2025
Workplace and Community Violence Cost Hospitals More than $18 Billion Annually
View Now
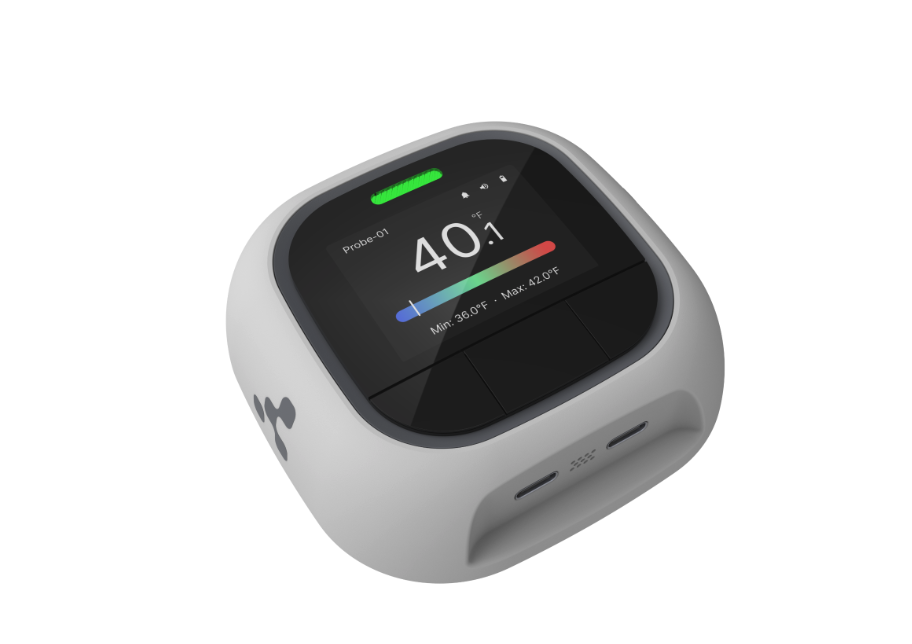
Blog
June 17, 2025
How it works: Temperature Monitoring Solution
View Now
Page
1