With the explosion of ecommerce and the changes in consumer behavior as a result of the COVID crisis, parcel delivery services are busier than ever before. In fact, many local, regional and even international carriers have broken one record after another in recent months.
- BLE Roll-Cage Tracking Solutions Benefits
- PostNL Digitizes 250,000 roll-cages with Bluetooth Beacons
- Are you ready for digital transformation?
While growth is certainly a good problem to have, it’s still a problem for operations that aren’t ready to quickly scale and can expose serious bottlenecks and process inefficiencies. This is one reason why the trend toward digitization of assets has quickly accelerated and become a must for delivery services around the world.
Parcel delivery teams face unique challenges that arise from the nature of the business. They struggle with a consistent lack of visibility into their inventory, including the lack of a mechanism for alerting them when roll-cages go missing, a problem that leads to significant losses. They also lack insight into the utilization of their assets and the location of specific roll-cages, which causes unnecessary bottlenecks and an inability to predict them ahead of time.
Bluetooth roll-cage tracking, on the other hand, offers a number of key solutions to this problem.
BLE Roll-Cage Tracking Solutions Benefits
PostNL recently announced that they are digitizing 250,000 roll-cages with Kontakt.io beacons. Bluetooth roll-cage tracking offers a number of advantages to postal services but also extends to other verticals. Here’s a list of the benefits they’ll enable that are applicable to many business contexts:
Want to learn more about the PostNL success project with BLE roll-cage beacons? Sign up for our live webinar (June 24, 2021 at 11am ET / 5pm CET) with Sander Haije, IoT Product Owner at PostNL.
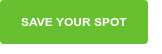
1. Get better insights into actual utilization of your equipment.
Bluetooth roll-cage tracking can give you better insights into the full utilization of your equipment: who is using it, how often it’s getting used, and how many units you have sitting empty at any given time. Bluetooth roll-cage tracking may, for example, let you see that you have empty units sitting in a warehouse that no one on the team is actually using and, as a result, you can decrease your overall costs by bringing in existing equipment and using it to full advantage, rather than trying to replace it.
Furthermore, you’ll get a look at which locations are fully utilizing the equipment they have available and, therefore, how you may want to change equipment placement in order to allow those locations greater efficiency and freedom. You may, for example, discover that adding a couple of roll-cages to one location can substantially increase their efficiency, while another does not need to utilize them at all.
Interested in purchasing roll-cage beacons? Contact us now!
2. Observe bottlenecks and supply chain challenges before they become more serious.
Bottlenecks and problems with your supply chain can leave you struggling to deliver inventory to your customers on time. Unfortunately, you may not be able to identify those challenges in time to stop them, which can leave your customers fighting to get the inventory or items they need at the right time.
With Kontakt.io’s Bluetooth roll-cage tracking beacons, on the other hand, you can often see those bottlenecks and supply chain challenges coming. Is there a shortage of inventory at one location? Chances are, it won’t move out as quickly if it all arrives at the same time. Is there a lot of inventory moving into one location at the same time? With Bluetooth tracking, you can identify those potential problems and move employees or equipment to compensate. This simple move can help you avoid long-term bottlenecks, often before customers realize the potential for delays.
3. Find each load unit with ease.
Losing inventory and equipment can prove catastrophic for your business. You may find yourself scrambling to find a specific customer’s items or paying out immense settlements in an effort to maintain customer satisfaction and make up for those mistakes. With our Bluetooth roll-cage tracking beacons, on the other hand, each roll-cage is automatically associated with a specific truck or warehouse location, which means that as long as you know which roll-cage the equipment is on, you can easily figure out where it is and redirect it to the right location if needed.
4. Get more information about your roll-cages in real time.
Did that roll-cage that just got stored in the warehouse come in fully loaded, or does it have extra room in it? Is that roll-cage with a customer’s vital equipment on it moving smoothly through the supply chain, or has it become stuck somewhere along the way? With Kontakt.io’s Bluetooth roll-cage tracking solution, you can get real-time insights into where each roll-cage is, what’s on it, and how it’s moving. Not only can this give you everything you need to reassure your customers, it can provide you with more insights into your processes, which may help you streamline them for your customers.
5. Cut your overall costs.
Tracking your roll-cages and what’s on them can often help you identify places where you can cut costs throughout your supply chain, whether it means sending out roll-cages fully loaded instead of half empty or making sure that those units take the most direct route possible to their end destination. This simple step can provide immense overall insights into your supply chain and your equipment needs, which can allow you to avoid unnecessary costs across your organization.
PostNL Digitizes 250,000 roll-cages with Bluetooth Beacons
One of our customers, PostNL, delivers approximately 1.1 million parcels and 8.1 million letters throughout the Benelux nations every day. With shops closed and people stuck at home because of the coronavirus pandemic, PostNL delivered a record number of packages in the Netherlands in 2020 : 337 million, which was 54 million more than in 2019.
It was this rapidly increasing flow of mail, and the proliferation of roll cages to handle it, that triggered the need to digitally quantify the journey of unique loading devices (ULDs), also known as roll cages, to provide better resolution in the tracking of the parcel’s journey and improve the quality of the information gathered at each step of the logistics chain.
Driving a multi-vendor IoT architecture, the PostNL project team was able to design the seamless flow of information from a beacon attached to a ULD in the field, through various mobile access points and other gateways, to the cloud, where it is processed and analyzed.
Kontakt.io and PostNL worked together to design an optimal tagging solution, providing previously unmatched service-free field life and connectivity performance. By attaching a motion-sensitive beaconing device to each ULD, PostNL is now able to track the location of the load unit, since it is associated with the truck or facility where it was delivered. Roll-cage journeys between customers and depots can now be planned more efficiently. Turnover speeds can also be increased due to faster identification of where the roll containers can best be used. On top of greater cost efficiency, there are environmental gains thanks to less empty space during transport.
Sander Heije, the Product Owner of IoT at PostNL added his perspective. “We went through a vendor selection process, identifying the leading companies and products that met our project settings. But when we started work, we knew we had to optimize the solution to our unique operating needs,” said Sander Heije, Product Owner of IoT. “The Kontakt.io team in Europe responded quickly and through a process of iteration and testing, we were able to start tagging our fleet of ULDs on schedule and move from a vision to a working solution we can use in our everyday operation,” added Sander.
The new real-time tracking system comes at a pivotal time for PostNL, whose parcel director, Liesbeth Kaashoek, estimates that as ecommerce continues to grow—about one-fifth of consumer spending in the Netherlands now occurs online—PostNL is looking to expand its daily capacity to two million packages by year end 2021.
Are you ready for digital transformation?
If you are facing logistics or other challenges that might respond to real-time tracking contact our sales team today and schedule a call with our experts today. On June 24, 2021, we will be hosting a live webinar with PostNL Sander Heije discussing the digital transformation they’ve done with Kontakt.io, what were the challenges and outcomes of non-digitized supply chains, how the project was implemented, why BLE was chosen, and what’s the path forward with IoT. Make sure to save your spot here.